Department of Accessible Prosthetics (DOAP)
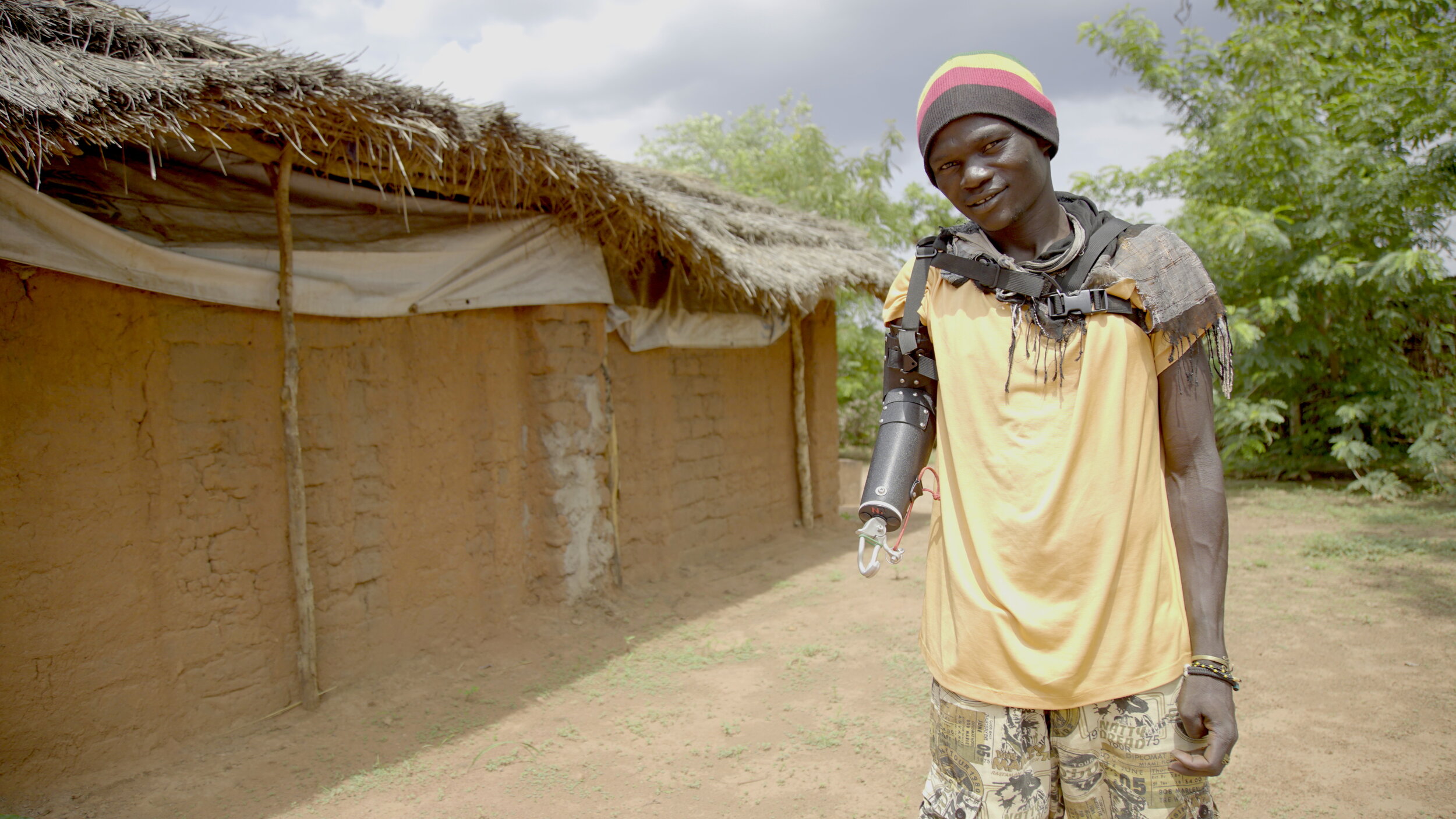
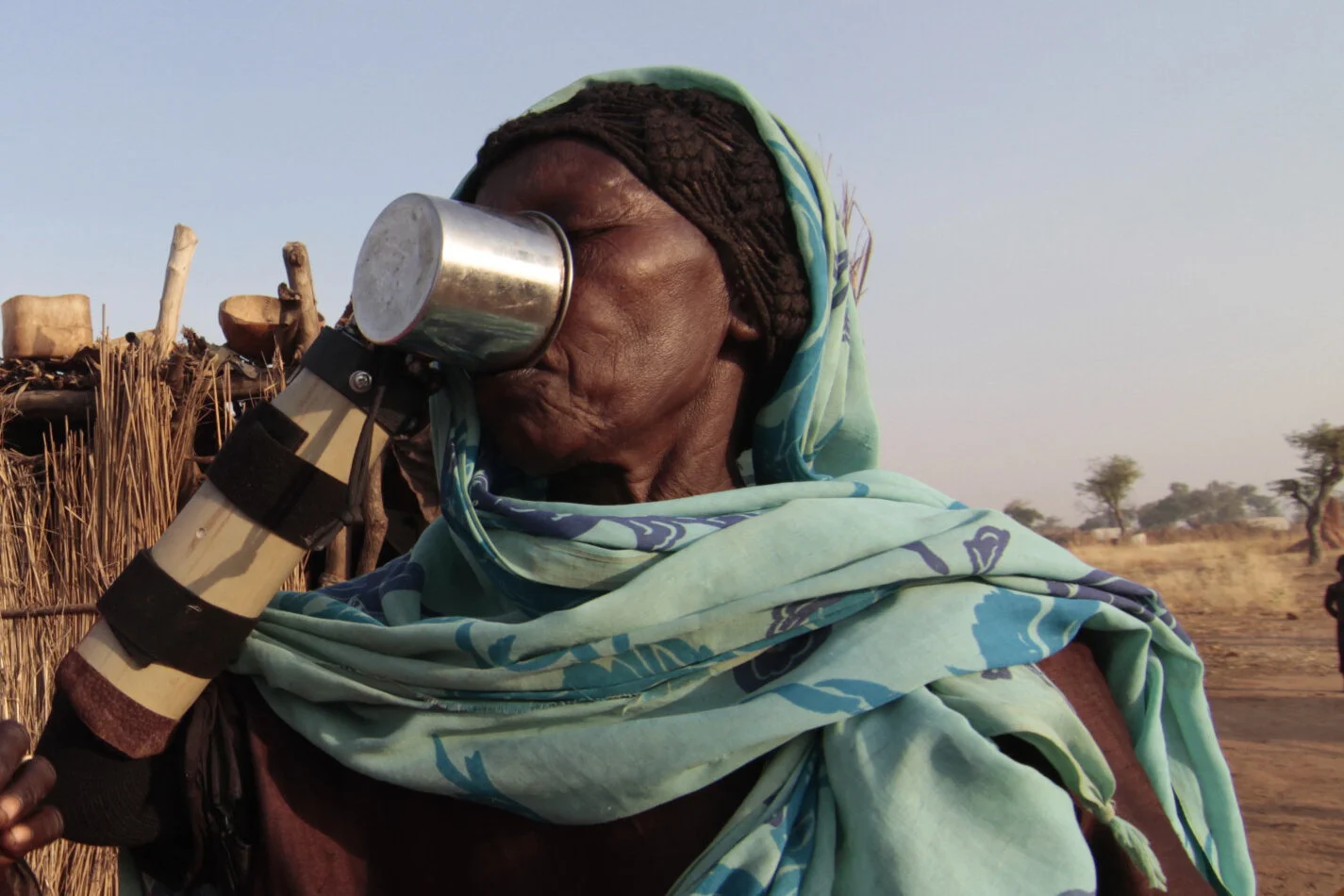

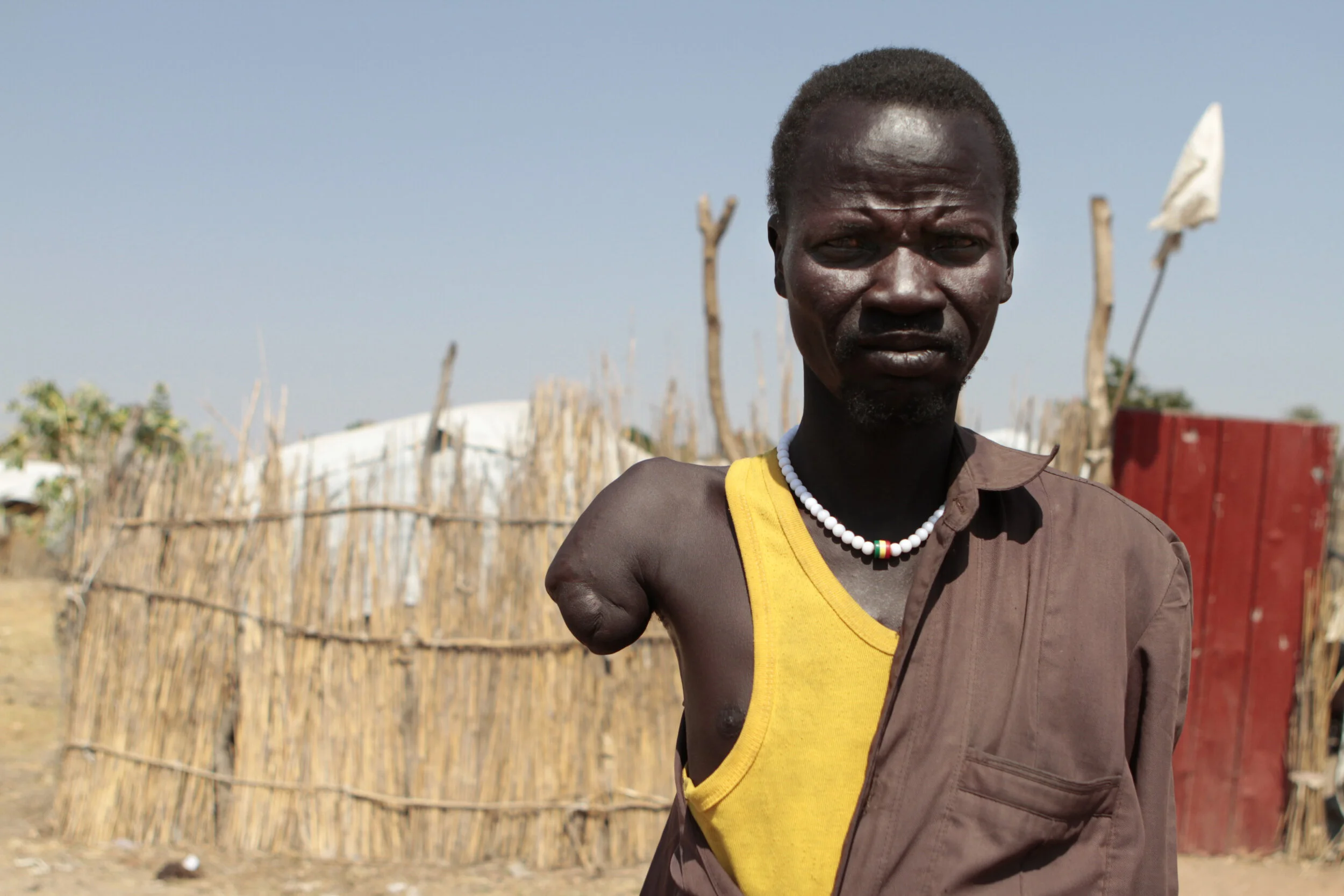
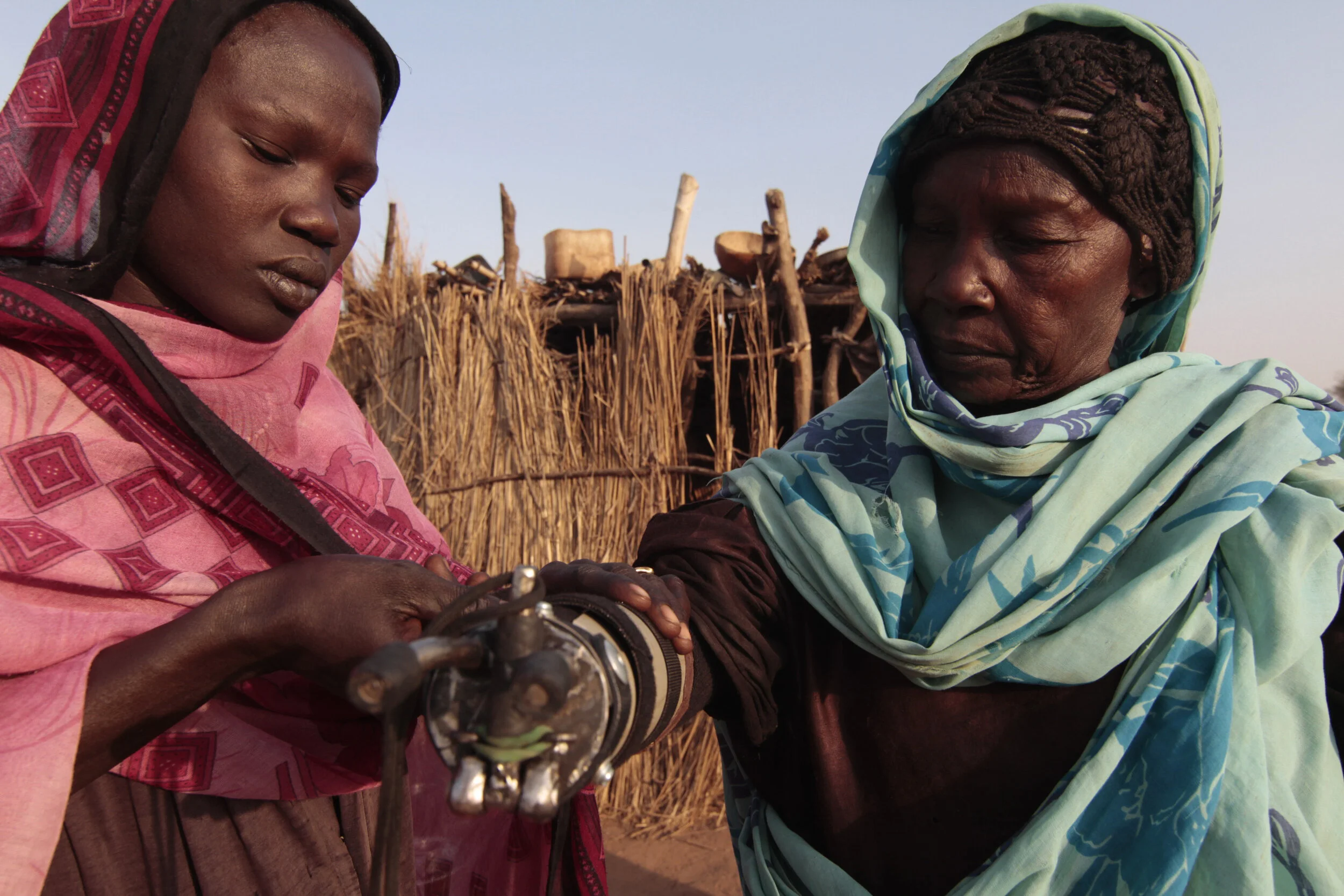
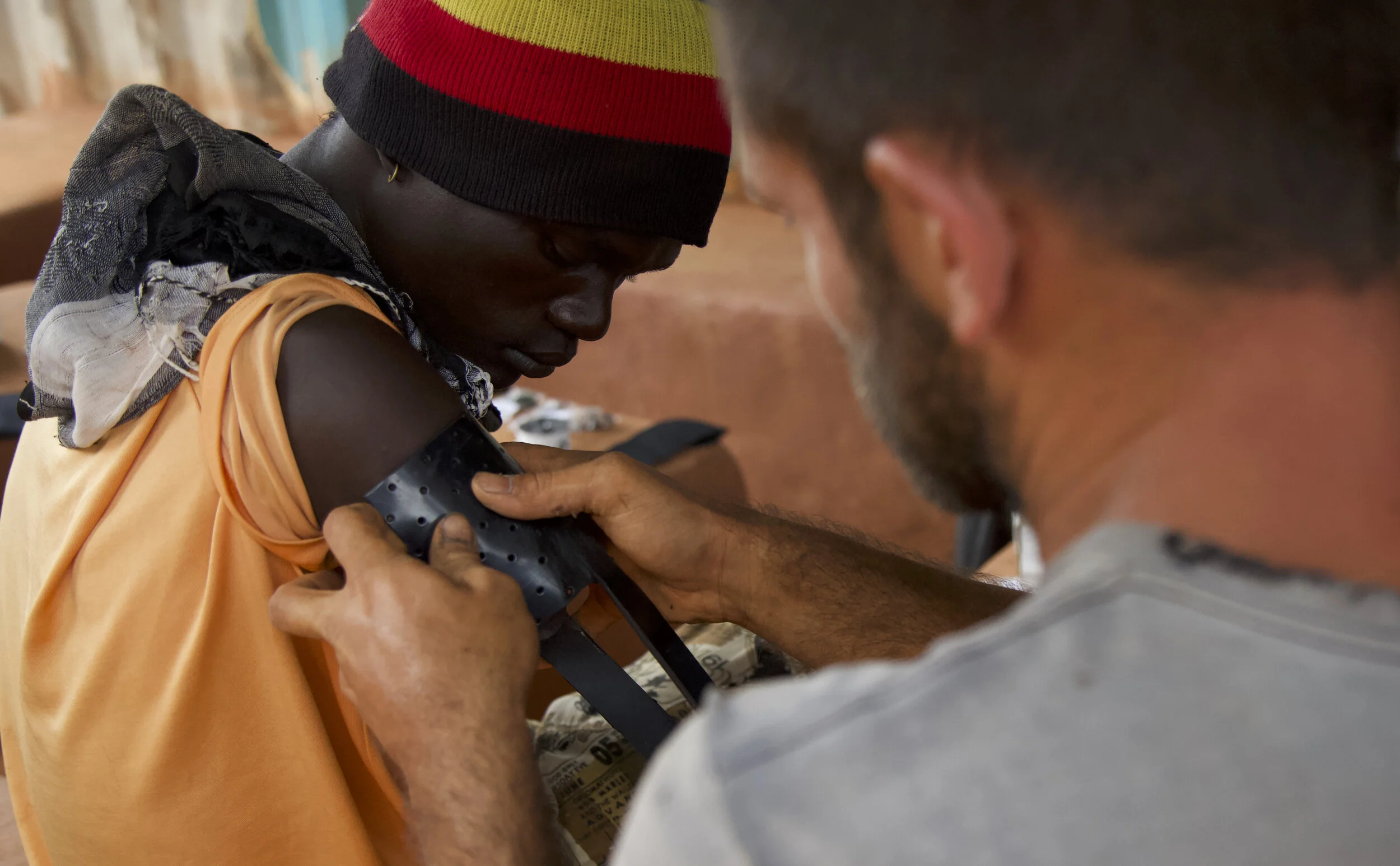

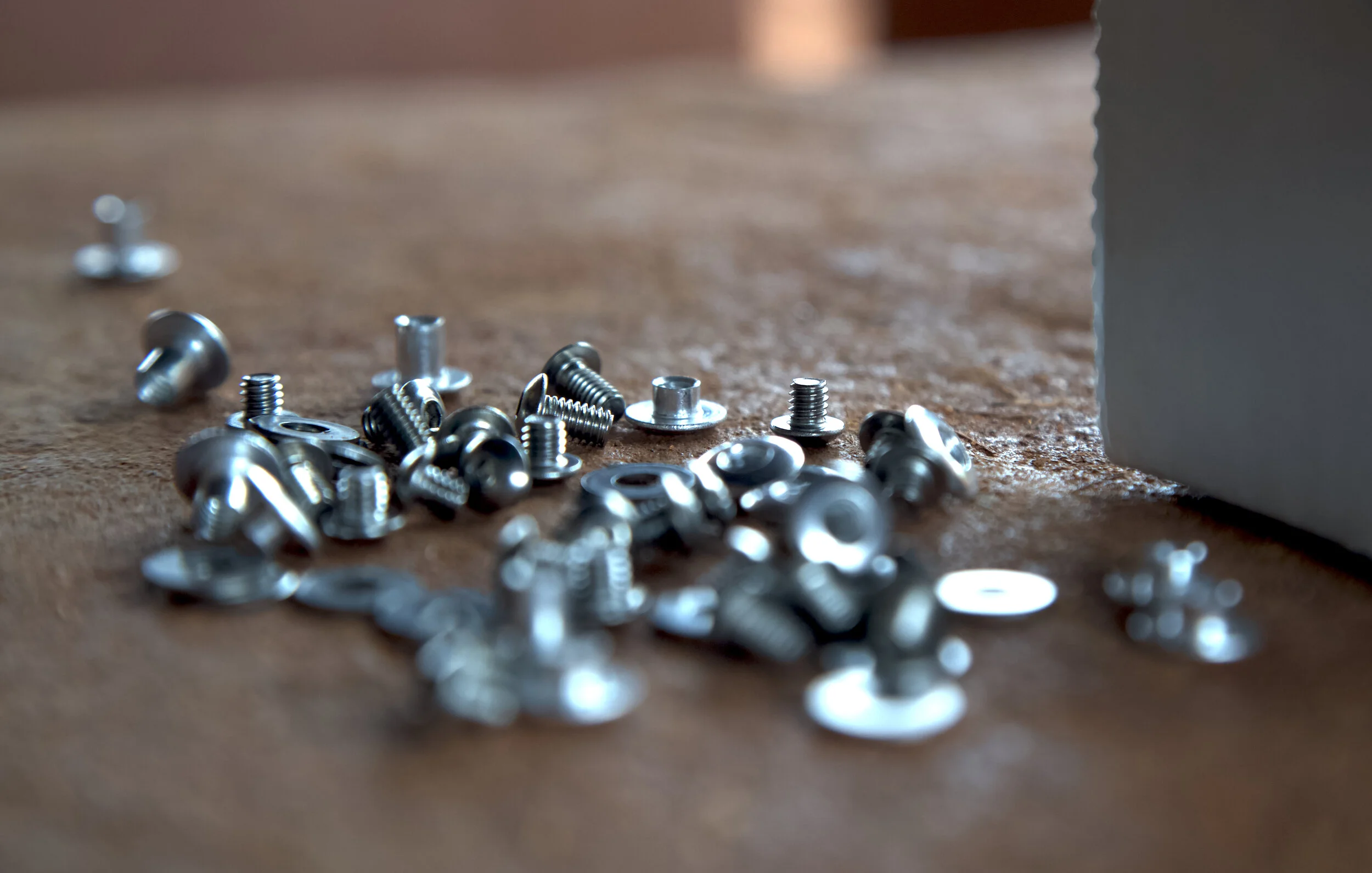


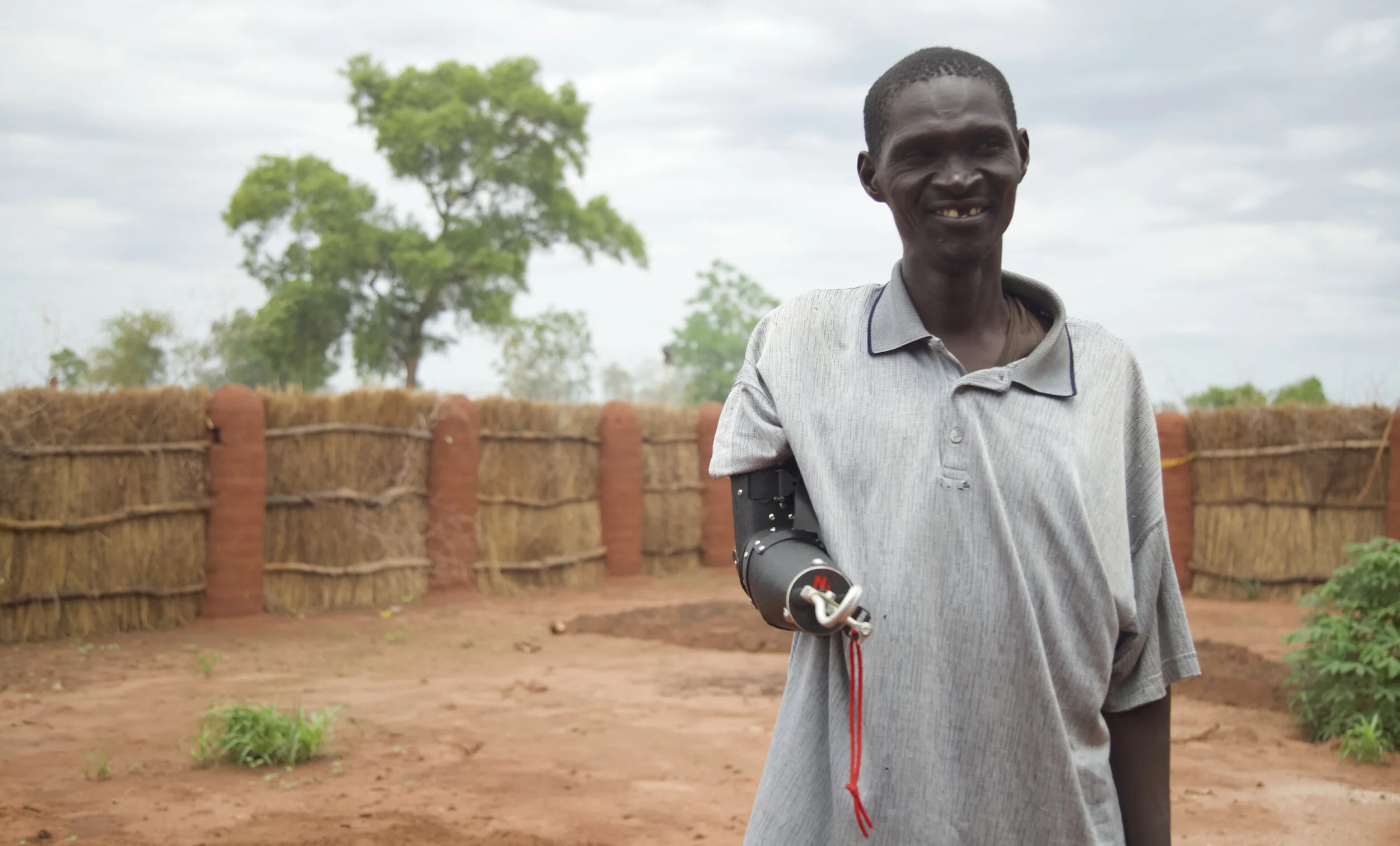
All photos by: Lesley D Onstott
This project is part of Not Impossible Labs.
Location: Yida Refugee Camp, Unity State, South Sudan
Date: R&D, Jan 2016 - March 2017; Field Pilot, Nov 2016 & March - July 2017
Challenge: Overcome environmental, societal and economic barriers to providing affordable and accessible prosthetic solutions for the most vulnerable amputees around the world.
80% of amputees cannot access a prosthetic.
In 2016, Tanzania saw a 150% increase in the number of surgeries with amputation.
Several factors inhibit the use of existing prosthetic solutions in the developing world:
◦ Cost
◦ Time-intensive fitting process
◦ Lack of trained professionals
◦ Lack of functionality for laborious work
Role: Project Lead, Field Researcher
Team: Mick Ebeling, Director; Eric Griffin, Lead Engineer; Jason Parliment, Asst Engineer; Field Testing: Michael Gathogo + Chris Low; Nuba Mountain Support: Mandi + Isaac
Hypotheses: A modular prosthetic solution with intuitive and straightforward design, a few hours of assembly and no need for electricity can provide a functioning prosthetic to an amputee in need, even in the most remote location.
If design and fabrication are created in a way that pairs utilitarian necessity with the most fundamental, historically impactful prosthetic technology, rehabilitation can be facilitated at scale.
Process | MVP + Field Test:
MVP: The prosthetic-in-a-box: a 3-pound box is filled with all the components needed to build and individually fit a prosthetic limb. The PIB is versatile and portable and requires no electricity to assemble and fit. It is the first complete, integrated limb system designed for even the most remote and resource-limited locations.
In each box:
3 sizes of pre-assembled fairings (the “arm”)
Various terminal devices (the “hand”)
Shoulder harness & velcro
2 sizes upper arm conversion kit
Pre-formed thermoplastic socket
Distal plug
Hardware
Tool kit
Prefabricated cable system
Each PIB is designed to provide two construction options: with or without the body-powered harness.
Field Test: For two weeks in November 2016, we set up a workspace from which we conducted trainings with hand-picked locals who worked in remote medical facilities. We carried out this training through testing beta prosthetics on amputees living in or near the displaced persons camp. We then took these learnings and implemented them ahead of a second pilot that was interspersed during our time in Yida for the “Build” project, March - July 2017. Individuals of all ages were able to volunteer to receive a PIB and provide feedback on its form and functionality.
Learnings: Numerous insights around ease of fitting process and choice of materials. One of the primary learnings was that form was more important than function to the majority of potential and final recipients.